
When planning a repair or purchase of furniture, you always want to learn more about existing materials, their advantages and disadvantages. Having comprehensive information, it is easier to understand what operating conditions these or those things are intended for, to calculate the approximate service life and make an informed choice. This article will focus on MDF - a substitute for solid wood, which is often confused with chipboards. Having a number of advantages, which will be described below, this material is excellent for construction, decoration, furniture, doors and decor.
What is MDF?
The abbreviation MDF is a transliteration of the English term Medium Density Fibreboard, which means “medium density fiberboard”.
This material consists of pressed, crushed sawdust mixed with binders. It is produced in sheets with a thickness of 3 mm to 6 cm. Furniture, construction and decoration elements, packaging and other things are made from fiberboards. In fact, it is an inexpensive wood substitute made from waste from the forestry industry.
Processing MDF is much easier than natural boards, in addition, it does not dry out, does not crack, retains heat perfectly and has good soundproofing properties. Compared to particle boards, this material is more environmentally friendly, since it contains much less formaldehyde resins.
The disadvantages of MDF include instability to moisture and mechanical stress, as well as rapid flammability. The life of MDF products under normal conditions is about 10 years.
How to make MDF panels
Sometimes MDF stands for “finely divided wood fraction” and this is not a mistake at all.
The fact is that for the production of this material, raw materials (wood chips, shavings, sawdust) are carefully crushed, turning almost into dust. To do this, they are first heated with steam to 100 ° C and brought to a humidity of 80%, after which they are placed in a defibrator and grind. Melamine-modified urea-formaldehyde resins and paraffin are added to the pulp. Then all this is dried for several seconds with hot air at an average temperature of 200 ° C and enters the hopper for compacting.
The resulting mixture is leveled with an ice rink along the conveyor, forming a continuous plate. Then, a press with a pressure of 350 MPa is lowered from above and the material is heated to 230 ° C. Under this influence, it fuses, condenses and gains strength. Subsequently, the pressure is reduced by about three times, and the thickness of the sheet is adjusted already without heating.
The cooled strip is ground and cut with a saw into plates. At the last stage, a decorative coating is applied.
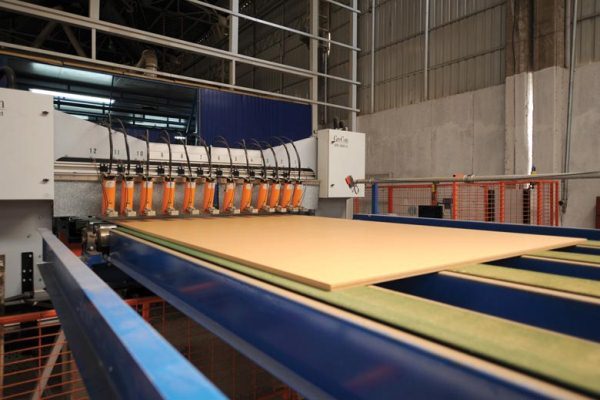
Types of MDF panels
Medium-density fibrous boards, which are used for the production of furniture and facial decoration, depending on the type of decorative coating are divided into laminated, painted and veneered.
Laminated
Lamination involves hot sticking on the surface of the MDF any decorative material. This can be tarred paper, melamine, and most often - PVC film. The front material adheres tightly to the base under the press, which ensures high aesthetics of the plates for the entire period of use. There are a huge number of laminate textures - like stone, leather, ivory, various fabrics, but the most popular are imitations of wood.
Painted
The use of modern paints and varnishes over the leveling primer layer makes it possible to make sparkling mirror-glossy or noble matte panels from grayish MDF sheets.This treatment is often used for kitchen furniture (which is important to protect from moisture), as well as other interior elements in the modern, hi-tech and minimalism styles.
Veneered
Veneer is a thin, beautiful cut of a natural tree. It sticks to the stove, giving it a complete resemblance to the original. Veneered MDF panels are used for the manufacture of doors, walls, chests of drawers and a huge number of other things.
In general, this is probably the most expensive type of finish, although the cost depends on the quality of the coating itself. In appearance and touch it is real wood, sometimes even rare, unusual species.
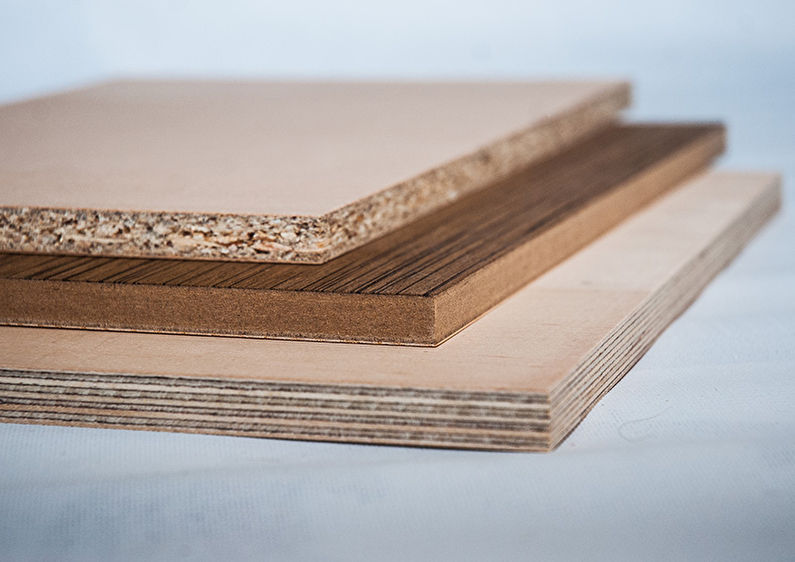
Properties and characteristics of MDF panels
Fiberboard in the modern world is no less popular than natural boards. There are a number of reasons for this, namely:
- strength - there is no air between the fibers of the pressed sheets, so the material does not crack or crumble, it keeps its shape for a long time;
- ease of processing, including decorative - it is easy to cut out any shapes from MDF, cut out voluminous jewelry and even give it soft bends using special technology;
- A large selection of front coatings, which allows you to find the perfect option for any interior.
After impregnating with special substances, laminating with a film or coating with latex water-repellent paint, MDF can be used even in humid rooms, such as a bathroom and kitchen. Products with the E1 marking are allowed for use in living rooms (this means that 100 grams of stove emit no more than 10 mg of formaldehyde, that is, the norm that is allowed by sanitary rules). In any case, there are several times more harmful fumes from particleboard.
MDF panels come in I class (without flaws) and II (slight aesthetic flaws, irregularities or slightly larger blotches are possible).
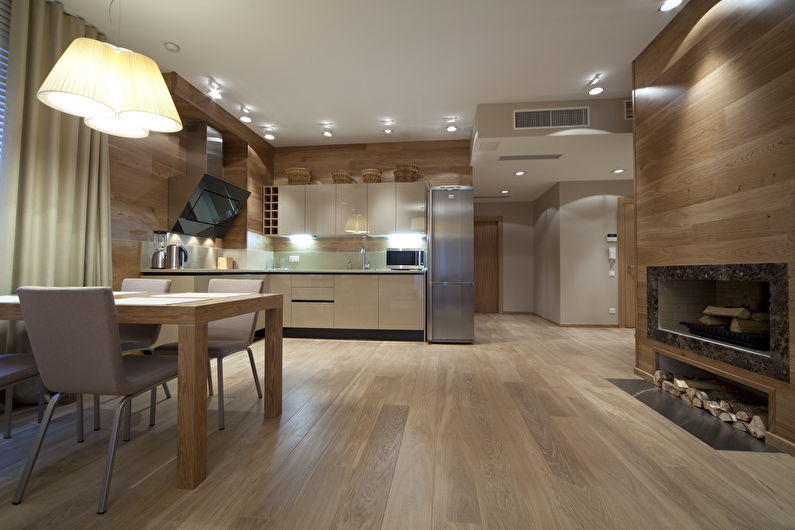
MDF application
Furniture
Products from medium-density fiberboards are a real find for everyone who wants to furnish their home, office or public institution with beautiful and high-quality furniture for a relatively low price.
As a rule, MDF is used for cabinet options - cabinets, headsets, shelves, tables, bedside tables, chests of drawers from this material look very modern and perfectly perform their functions.
However, often it also forms the basis of sofas, soft chairs, beds. Covered with laminate or veneer, with embossed patterns or interestingly painted, MDF furniture will help create a cozy and warm atmosphere anywhere.
Construction and repair
MDF copes with the role of a universal substitute for wood and in the arrangement of buildings. Beams, partitions are made from such plates, they sheathe ceilings, insulate walls, plinths, corners, door frames, doors, stairs, railings and window sills are made.
But where to use such panels is not worth it, it is on the floor (they are quite soft and can be deformed), as well as in the exterior decoration and in rooms with very high humidity.
Cutting out any shape or cutting a pattern from MDF is not difficult even for those who have never worked with wood and do not have special machines. This occupation is somewhat reminiscent of drywall processing.
When making manipulations with MDF, it is worth remembering that it does not allow repeated use of self-tapping screws and nails. If you need to make such a fastening, holes are first drilled in the material, and then the elements are connected using bolts and nuts.